パーツフィーダーの動作原理
パーツフィーダーは大量のワーク(部品・部材)をボウルの振動とアタッチメントの誘導で一気に同一の方向・姿勢に整列させて次工程の機械(組立機・包装機・検査機等)に供給する装置です。手作業での部品供給に比べて作業の速度と正確性が飛躍的に上がり生産性の向上に貢献いたします。
パーツフィーダーのバリエーション
パーツフィーダーは用途や追加機能、設置する場所等お客様の工場の工程やご都合に合わせたバリエーションが存在いたします。
-
リターンフィーダー
リターンフィーダーは小型のパーツフィーダーで主に広い設置場所が確保出来ない場合に使用されます。
非常に小さい上に安価というメリットの反面、排出能力(タクト)があまり高くないというデメリットがあります。
カメラを装着して画像処理検査装置にも出来ますし自動部品供給装置に組み込む事も可能です。 -
画像処理検査装置
パーツフィーダーに積んだカメラと画像処理検査装置でワークの傷や汚れの検査や姿勢・状態(裏表や位置)の判定を行います。ワークの整列・排出と平行してチェック作業が行われるので作業時間が短縮され生産力の向上につながります。
また、作業員の目視に頼っていた検査作業を機械化することで精度が飛躍的にアップし作業ミスを防ぎつつコストの削減にも貢献いたします。 -
自動部品供給装置
ワークの方向と姿勢を整えて排出するパーツフィーダーと次の工程の機械(組み立て・包装・梱包・袋詰め・カウント等)を一体化した装置になります。
全ての工程をひとつの装置にまとめることで小型化が可能となり設置面積が大幅に縮小されるので工場への組み込みも容易になります。
さらに、動作の安定性も向上するので作業効率のアップが望めます。
製品仕様を決める3つのポイント
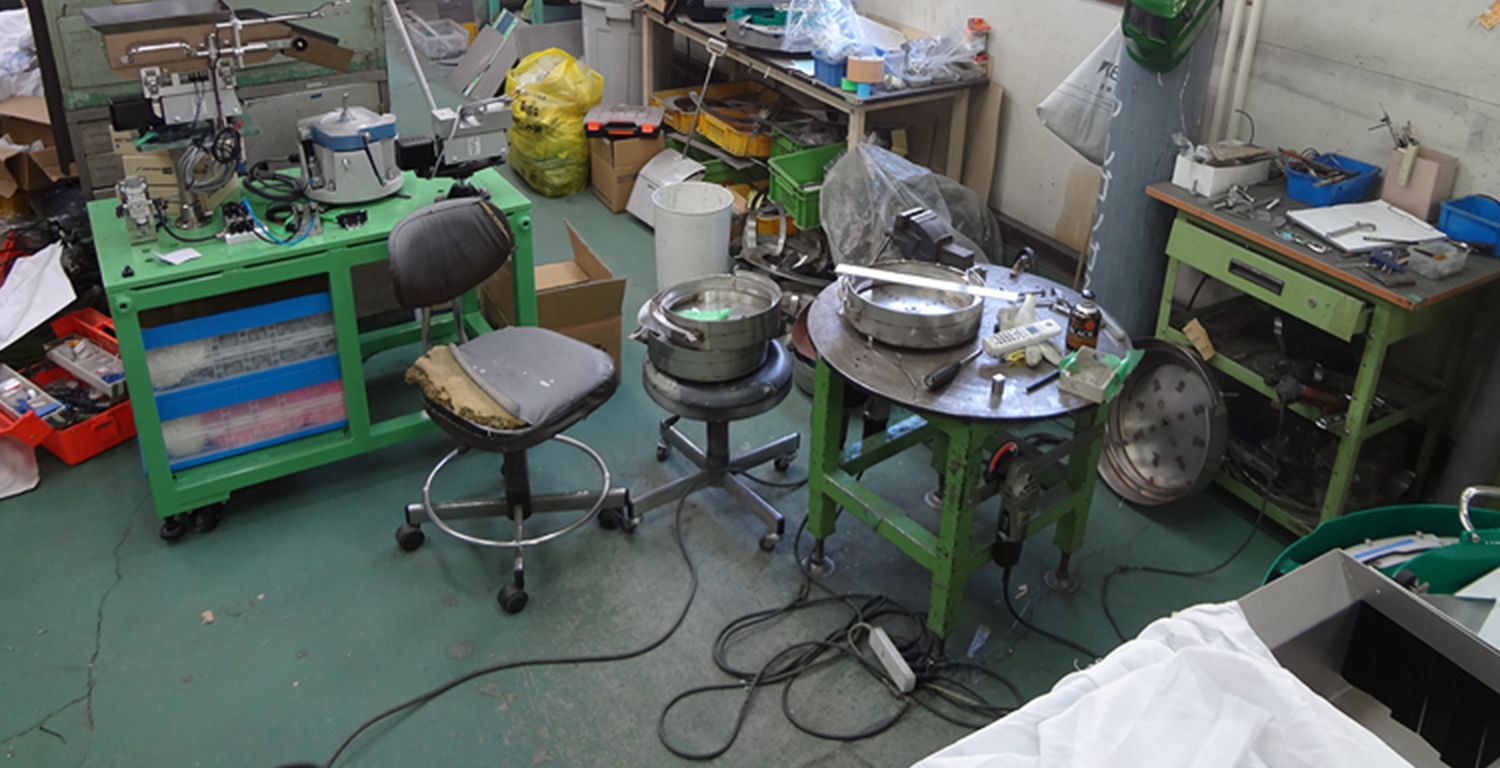
-
A. ワークの特性
パーツフィーダーの設計の基本は整列・排出させるワークの特性の分析から始まります。まず、ワークの材質・重量・サイズ等に最適なボウルを決定し、それに合う振動体・コントローラー・直進フィーダー等必要な部品を選定して組んでいきます。
-
B. 排出能力
排出能力(供給能力)は1分間にパーツフィーダーより次工程の機械へ供給するワークの個数を表します。より高い排出能力が必要な場合は多列排出という手段がありますが、列により供給数にバラツキが発生するというデメリットもあります。
-
C. 様々な対策
ワークの形状が複雑で絡みやすい・傷つきやすい・静電気に弱い・付着物がある等整列と排出の障害になる場合には様々な対策が必要になります。他にも複数のパーツフィーダーを組み合わせる場合には共振対策が、騒音が問題の場合はボウルの表面処理が必要です。
パーツフィーダーの各部名称と働き
-
1振動体(駆動部)
パーツフィーダーの要となる振動を発生させる装置です。電磁石のONとOFFで生じる力を板バネで増幅して振動を発生させます。電磁石の個数や板バネの材質・形状や枚数・角度、電磁石と板バネの幅等を変更する事で振動量の調整が可能です。
振動体は電磁石を利用した「電磁式」が主流ですが、圧電素子を利用した「ピエゾ式」も普及しています。 -
2ホッパー
ボウル内のワーク不足を検知し自動的に補充、一定量を保ち排出能力を安定させると同時に入れ過ぎによるワークの傷や汚れを防ぐ効果もあります。 ホッパーの選定はワークのサイズ・パーツフィーダーの排出能力・自動化したい時間(h)・容積(L)等から算出します。「電磁式」「コンベアー式」「シリンダー式」等様々な種類がありワークの特性や設備スペース等を勘案して使い分けます。
-
3ボウル
ワークを入れる容器で、振動体で振動させワークの方向・姿勢を一定に整えます。ボウルには側面が均一でアタッチメントの選択が多彩な「円筒型」と側面がすり鉢状の「段付型」があり、螺旋の方向は「時計方向(R)」「反時計方向(L)」があります。また、ワークの特性に合わせてボウルの巻き数を増減して搬送面(トラック)の傾斜角度を変更し最適な状態に調整いたします。
-
4センサー
パーツフィーダーでは作業を自動化する為に様々な用途でセンサーを使用いたします。
ボウル内のワークが減少してきたらセンサーが検知してホッパーから自動的にワークを追加いたします。
また、アタッチメント内でのワークの姿勢制御やシュート内でのワークの詰まりや溢れの確認等にも用いられます。 -
5アタッチメント
組立機・包装機・検査機等の次工程の機械に送るためにボウル内のワークの向きを同一方向に整列させる機構でツーリングとも呼ばれます。ワークの方向・姿勢の正誤判別はワークの形状や重心の違いで判断する方法とセンサーやエアーを用いる方法があります。
アタッチメント加工はパーツフィーダーにおいて最も製作者の技術力が問われる部分でもあります。 -
6シュート
整列したワークをパッシングライン(次工程の機械への受け渡し部)まで送る機構で通常、直進フィーダーとの組み合わせで使用されます。
ワークが硬い場合にはSUS材を使用して更に表面を窒化し硬度を上げる必要があります。シュートの表面に傷を付けて摩擦抵抗を抑える処理やワークの自重で滑り台の様に送る傾斜シュートもございます。 -
7直進フィーダー
シュートに振動を与える小型の振動体です。直進フィーダーには固定式・ゴム足方式・板バネ式等、様々な種類がありますがシュートの長さやワークの重量を考慮してワークをスムーズに送れる機種を選定します。
また、設置場所の強度不足は排出能力の低下を招きますが机のような強度に問題がある設置場所でも振動が安定する直進フィーダーもございます。 -
8架台(台板)
ワークを整列・排出する為に振動体や直進フィーダーで発生させる強烈な振動を支えるのが架台(台板)です。
架台には頑丈な鉄製と軽量のアルミ製がありますが信和技研では安定した排出能力を発揮させる為にも厚み(16mm以上を推奨)のある鉄製の架台をお勧めしております。 -
9コントローラー
パーツフィーダーを文字通りコントロールする装置で起動や停止をはじめ、周波数による振動の強弱、センサーやエアーを調整することで排出能力の制御も行います。
様々な方式のコントローラーがありますが「インバーター式」が主流です。